Quality Control Best Practices for Small Businesses
12 Best Practices in Quality Control for Small Businesses
Regardless of the size of any business, quality control is essential for the success and sustainability of any organization. For small businesses, maintaining high-quality products and services is not only a matter of compliance but also a strategic necessity. Customers increasingly demand quality, and one negative experience can lead to lost sales and damaged reputations. To thrive, small businesses must embrace quality control best practices and integrate them into their operations. Here in this post, we’ll be explaining how small business quality control practices can help in long-term success.
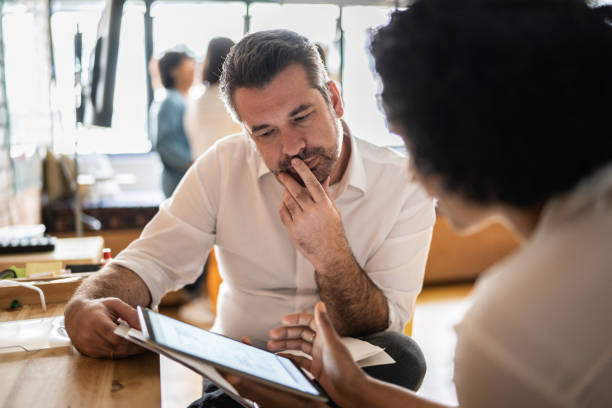
Quality Control in Small Businesses
Quality control, often synonymous with quality management, includes a set of systematic processes and practices aimed at ensuring that products or services consistently meet or exceed customer expectations. Quality control should be the top priority. For small businesses, quality control, or quality management is about more than just meeting industry standards; it’s about differentiating themselves from competitors and building a loyal customer base. Below are some key best practices tailored to small businesses:
Document Standard Operating Procedures (SOPs)
Small businesses should document their processes and procedures to ensure consistency. SOPs serve as guides for employees, helping them understand their roles and responsibilities in maintaining quality.
Implement Quality Metrics
Define key performance indicators (KPIs) related to quality and track them regularly. Metrics could include defect rates, customer complaints, on-time delivery, and product/service performance. Analyzing these data points helps identify areas for improvement.
Employee Training and Involvement
Well-trained employees are more likely to produce quality work. Small businesses should invest in training programs that educate employees on quality standards, processes, and the importance of their role in maintaining quality. Encouraging employees to contribute ideas for process improvement fosters a culture of continuous quality enhancement.
Supplier Quality Management
Small businesses often rely on suppliers for materials or components. It’s crucial to establish strong relationships with reliable suppliers who share the commitment to quality. Regularly assess supplier performance and conduct audits when necessary.
Customer Feedback
Actively seek and analyze customer feedback. Whether through surveys, reviews, or direct communication, understanding customer perceptions is essential for improving products or services. Address customer complaints promptly and use them as opportunities for improvement.
Root Cause Analysis
It is one of the most important small business quality control practices, which is often overlooked. When quality issues arise, small businesses should perform root cause analysis to identify the underlying reasons. This systematic approach helps prevent recurring problems and drives process improvement.
Quality Control Tools
Utilize quality management tools and methodologies such as Six Sigma, Total Quality Management (TQM), or the Plan-Do-Check-Act (PDCA) cycle. These frameworks provide structured approaches to quality improvement.
Regular Audits and Inspections
Conduct internal audits and inspections to ensure compliance with quality standards and processes. These assessments should cover all aspects of the business, from production to customer service.
Technology Adoption
- Leverage technology to enhance quality control efforts. Implement quality management software or tools that enable real-time monitoring, data analysis, and reporting. Automation can streamline processes, reduce errors, and provide valuable insights for decision-making.
Continuous Improvement:
Embrace a philosophy of continuous improvement. Small business’s quality control is not a one-time effort but an ongoing journey. Small businesses should regularly review and refine their processes to adapt to changing market conditions and customer needs.
Risk Assessment and Management
Small businesses should proactively identify potential risks that could impact product or service quality. This includes assessing risks related to supply chain disruptions, process failures, and regulatory changes. Developing risk mitigation strategies and contingency plans ensure preparedness for unforeseen challenges.
Feedback Loops
Establish feedback loops within the organization to facilitate the sharing of insights and lessons learned. Encourage employees to report quality-related issues, suggest improvements, and provide feedback on existing processes. Regularly review this feedback to drive continuous improvement.
By incorporating these additional practices into their quality control framework, small businesses can further strengthen their commitment to delivering high-quality products. This will also help them maintain a competitive edge in their respective markets.
Benefits of Quality Control for Small Businesses
Implementing effective quality control practices can yield numerous benefits for small businesses:
Enhanced Reputation: Consistently delivering high-quality products or services builds a positive reputation in the marketplace, leading to increased customer trust and loyalty.
Identifying Innovation on Time: Quality control fosters a culture of innovation within small businesses. By regularly assessing and improving processes, products, and services, companies can identify opportunities for innovation and stay ahead of market trends. This proactive approach enables small businesses to develop new offerings and maintain relevance in a rapidly evolving business landscape.
Stronger Supplier Relationships: Small businesses that prioritize quality control often require their suppliers to adhere to similar quality standards. This commitment to quality can lead to stronger, more reliable relationships with suppliers. Suppliers who meet quality expectations contribute to smoother operations and reliable access to materials or components, reducing supply chain disruptions.
Adaptability to Market Changes: Small businesses that have established robust quality control processes are better equipped to adapt to changing market conditions. Whether facing shifts in customer preferences, emerging industry regulations, or economic fluctuations, these businesses can quickly adjust their processes and offerings to remain competitive and resilient in the face of uncertainty.
Cost Savings: Quality control helps identify and rectify defects early in the production process, reducing waste, rework, and the overall cost of poor quality.
Competitive Advantage: Small businesses that prioritize quality control can differentiate themselves in the market, positioning themselves as providers of superior products or services.
Customer Satisfaction: Meeting or exceeding customer expectations in terms of quality leads to higher customer satisfaction, positive word-of-mouth, and repeat business.
Reduced Risks: Effective quality control minimizes the risk of legal and regulatory issues, ensuring compliance with industry standards and regulations.
Operational Efficiency: Streamlined processes and optimized operations result in increased efficiency and competitiveness within the industry.
Final Thoughts
For small businesses, quality control is not an option; it’s a necessity. By embracing these best practices for small business quality control, It becomes easy to enhance product and service quality, reduce costs, and gain a competitive edge in the market. A commitment to quality not only satisfies customer expectations but also fosters trust, loyalty, and long-term success. Nowadays, when quality is non-negotiable, small businesses that prioritize quality management are best positioned for growth and sustainability.