8 Common Quality Control Challenges And Solutions
Navigating 8 Complex Quality Control Challenges: Effective Solutions for Navigating Them
As manufacturers have successfully coped with their evolution, they are experiencing a set of unprecedented quality control challenges and opportunities that hold the potential to reshape their businesses. A few difficult situations like covid 19 have led to severe vulnerabilities present in global supply chains, compelling companies to reevaluate their operational processes and strive for greater resilience. Within these changes, the significance of quality control has come to the forefront. Uniquely positioned at the central point of operations, engineering, and quality management, QA/QC professionals have all the necessary tools and expertise to guide organizations through the manufacturing challenges connected to this transformation. So, one cannot deny the significance of quality control and the challenges that come along with it.
Quality control is one of the most important elements towards conquering manufacturing excellence. Moreover, the role of the quality control process is to consistently deliver high-quality products so that manufacturers and businesses can earn and maintain the trust of their customers. However, the path to achieving consistent quality can be fraught with challenges. In this blog, we will explore 8 common QC challenges with practical quality solutions to help businesses navigate them effectively.
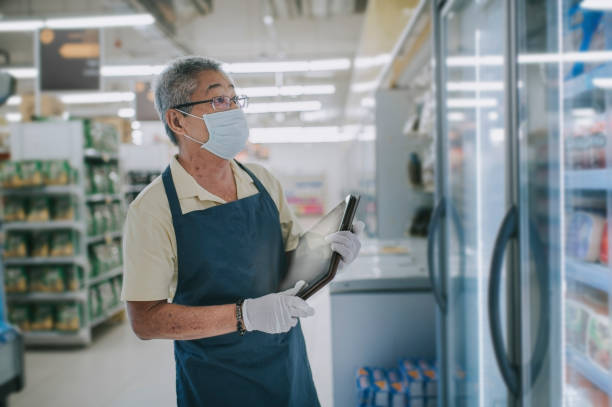
1. Challenge: Inconsistent Product Quality
Solution: Standardize Processes and Training
Inconsistent product quality can arise from variations in manufacturing processes and workforce skills. To address this challenge, businesses should standardize their manufacturing processes and invest in comprehensive training programs. By establishing clear, standardized procedures and providing ongoing training for employees, companies can ensure that every product adheres to the same quality standards.
2. Challenge: Lack of Product Knowledge
Solution: Develop Training Programs for Mitigating Production Challenges
In many cases, comprehensive details of a product’s functionality is confined to the product team and top-level executives. This knowledge gap exposes your workforce to potential production issues that could have been managed with a better understanding of the product.
So, the solution to this quality control challenge is to develop an in-depth training program dedicated to your product. This initiative serves a dual purpose of proactively mitigating production challenges and providing a valuable reference point for employees seeking clarification or guidance regarding the product. Key questions that your training should address include: What is the product, and what specific issue does it resolve?
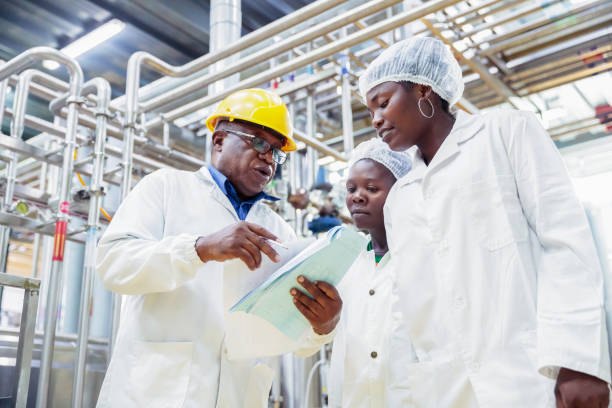
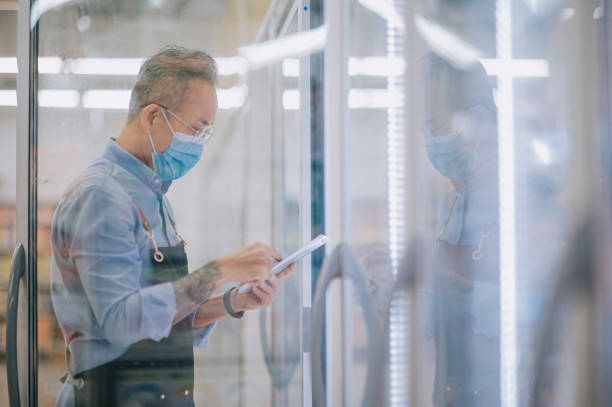
3. Challenge: No Proper Documentation
Solution: Create Proper Documentation from Ideation to Manufacturing
From product concept to manufacturing, the crucial information throughout the process often remains unrecorded. Product managers may convey one set of instructions, while engineers advocate for an alternative approach, all without communicating with one another. Inadequate product documentation can result in inconsistent product quality, manufacturing complications, and customer dissatisfaction.
To counter this challenge we have an effective quality solution. There is a need to thoroughly document every aspect of the product, from its inception to the manufacturing stage. Ensure that all decision-makers are well-informed about each decision and the reason behind the chosen processes. Create a structured presentation that outlines the entire product documentation journey for better clarity.
4. Challenge: Rising Manufacturing Costs
Solution: Implement Lean Manufacturing Practices
Escalating manufacturing costs can erode profitability. Implementing lean manufacturing practices is an effective solution. By optimizing processes, reducing waste, and maximizing resource efficiency, businesses can streamline operations and reduce costs. Lean practices not only enhance cost-effectiveness but also improve overall quality and customer satisfaction.
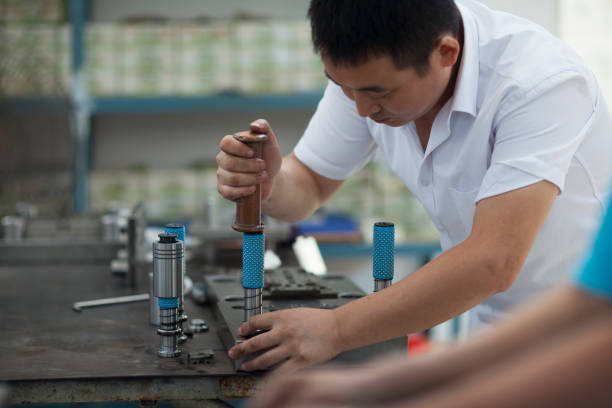
5. Challenge: Compromising Data Security and Traceability
Solution: Integrating Latest Technologies to Track and Access Important Data
The rapid digitalization of processes necessitates robust cybersecurity and data traceability measures, particularly for quality control departments handling sensitive product information. They must integrate their departments into the organization’s comprehensive cybersecurity strategy. This includes regular risk assessments, employee training, and stringent access controls.
Moreover, in addition to adhering to general cybersecurity best practices in manufacturing, quality control departments should prioritize comprehensive data traceability within their quality systems. This step is vital for safeguarding data integrity, reducing human interference in data management, and preventing issues such as materials testing fraud.
Utilizing technologies like RFID and barcode scanning can streamline data entry, minimizing errors. Furthermore, materials and component testing systems should facilitate complete traceability of test results, empowering quality professionals to effortlessly track the history of specimens, component numbers, or material lots.
6. Challenge: Meeting Stringent Compliance Requirements
Solution: Robust Compliance Management Systems
Stringent regulatory and industry-specific compliance requirements can pose significant challenges. To ensure compliance, businesses should implement robust compliance management systems. These systems streamline documentation, audits, and reporting, making it easier to meet regulatory obligations. Regularly updating compliance procedures and staying informed about changing regulations is also crucial.
7. Challenge: Identifying and Addressing Defects
Solution: Implement Effective Testing and Inspection Protocols
Identifying and addressing defects is one of the fundamental quality control challenges. Effective testing and inspection protocols are essential solutions. By conducting thorough product testing at various stages of production and implementing stringent inspection processes, businesses can detect defects early and take corrective measures promptly. This not only reduces production costs but also prevents defective products from reaching customers.
8. Challenge: Maintaining Consistent Supplier Quality
Solution: Establish Strong Supplier Relationships and Audits
Maintaining consistent supplier quality is a common challenge, particularly in global supply chains. Establishing strong relationships with suppliers and conducting regular supplier audits are essential solutions. By fostering open communication and collaboration with suppliers, businesses can align their quality standards and expectations. Conducting supplier audits ensures that suppliers adhere to these standards, mitigating quality risks.
In conclusion, quality control challenges are inherent in manufacturing, but they are not impossible to handle. The ultimate goal of quality solutions is to achieve and maintain a consistent level of product quality that not only meets but often exceeds predefined standards. With the right strategies and quality solutions in place, businesses can navigate these challenges effectively, ensuring consistent product quality, compliance, and cost-efficiency. Prioritizing quality control not only safeguards brand reputation but also fosters customer trust and long-term success in a competitive market. This, in turn, ensures that the products leaving the manufacturing facility are reliable, safe, and fulfill customer expectations. Simultaneously, the emphasis on quality control plays a vital role in facilitating compliance with regulatory requirements, safeguarding against potential legal issues, and promoting cost-efficiency.